What is Flex Pipe?
From potholes to crumbling pavement, rough roads can cause your truck’s engine to vibrate and shake. These vibrations can stress the components of the exhaust system and lead to premature failure. To mitigate the effects of engine vibrations, flex pipe is used in the exhaust system to absorb the reverberations and allow the engine and exhaust components to move without breaking or cracking.
Tips for Replacing Flex Pipe
Properly functioning flex pipe is key to exhaust system health. When it's time to replace flex pipe, keep these tips on the proper way to measure, cut and install flex pipe in mind for a successful installation. Following these techniques will prevent issues such as premature failure and unraveling of the flex pipe.
Measuring Tips
Measure the existing flex pipe that you want to replace. Measure the distance from the intermediate pipe to the elbow.
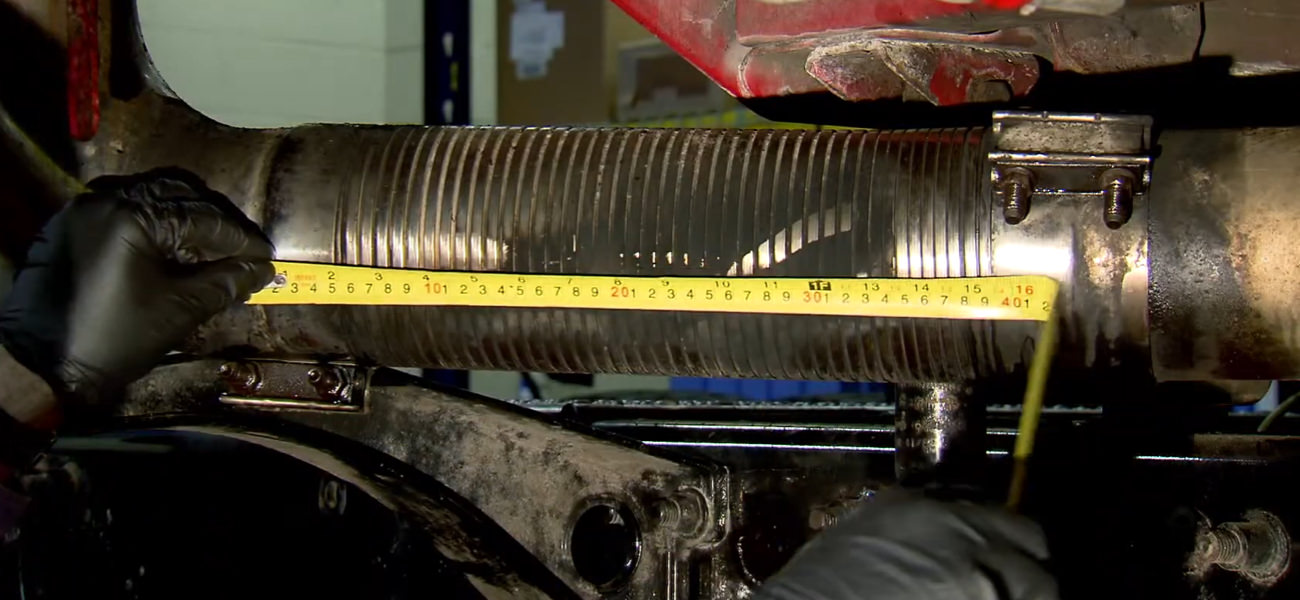
Tips: On some applications, it’s important to allow for travel in the cab suspension. To do this, disconnect the air leveling valve and manually force it through full extension and compression.
Make sure you inspect any engine or transmission mounts and exhaust hangers for wear which could allow excessive movement of the exhaust system resulting in stress to the flex section.
Make sure to add 6" to the overall length to allow for 3" overlap at each connection.
When comparing the new pipe to the pipe you’re replacing, make sure both parts are fully extended.
When measuring and cutting, keep the open side of the flex pipe to your right.
To determine the open end, turn the end of the pipe toward you and look for the rings to wrap on top in a counterclockwise direction. You’ll be cutting to the left, allowing you to cut through the closed section of pipe.
Cutting Tips
Wrap the area to be cut with duct tape and use a marker to draw a cut guide on the tape.
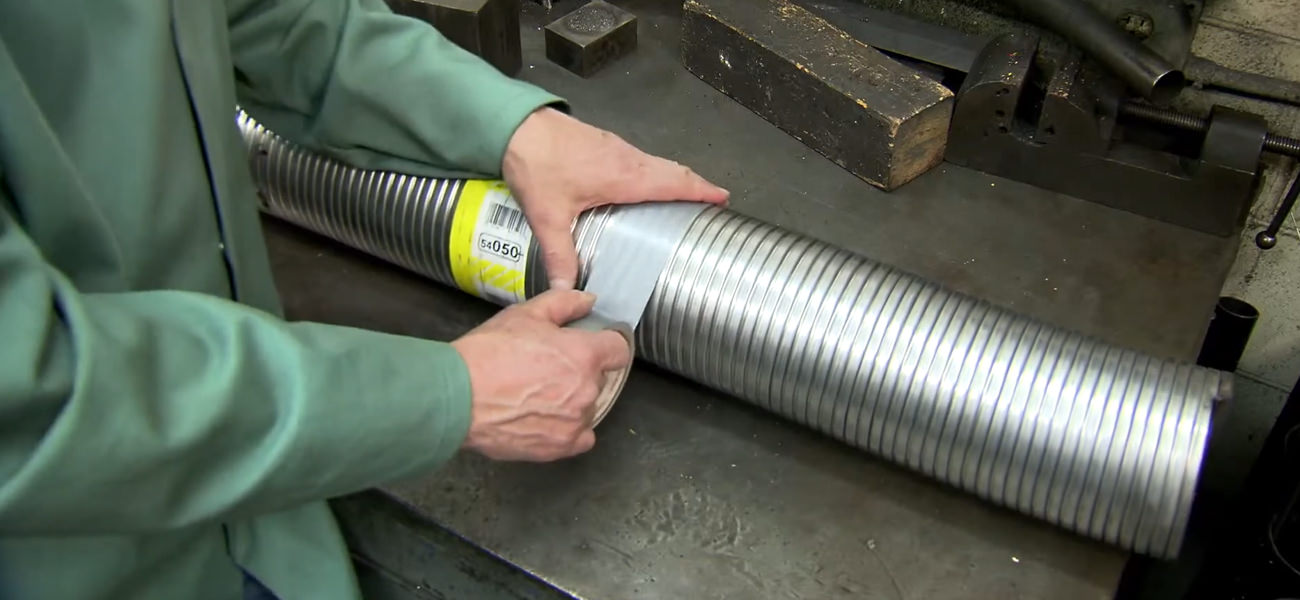
Other methods for getting a guide mark on the pipe include apply several tack welds around the intended cut or putting veral punch marks around the intended cut with amandrel or backup pipe inside the tubing.
Methods for Cutting Flex Pipe
There are three ways to cut flex pipe, choose the method that suits your shop.
Plasma cutter – Leaves a smooth edge without burrs.
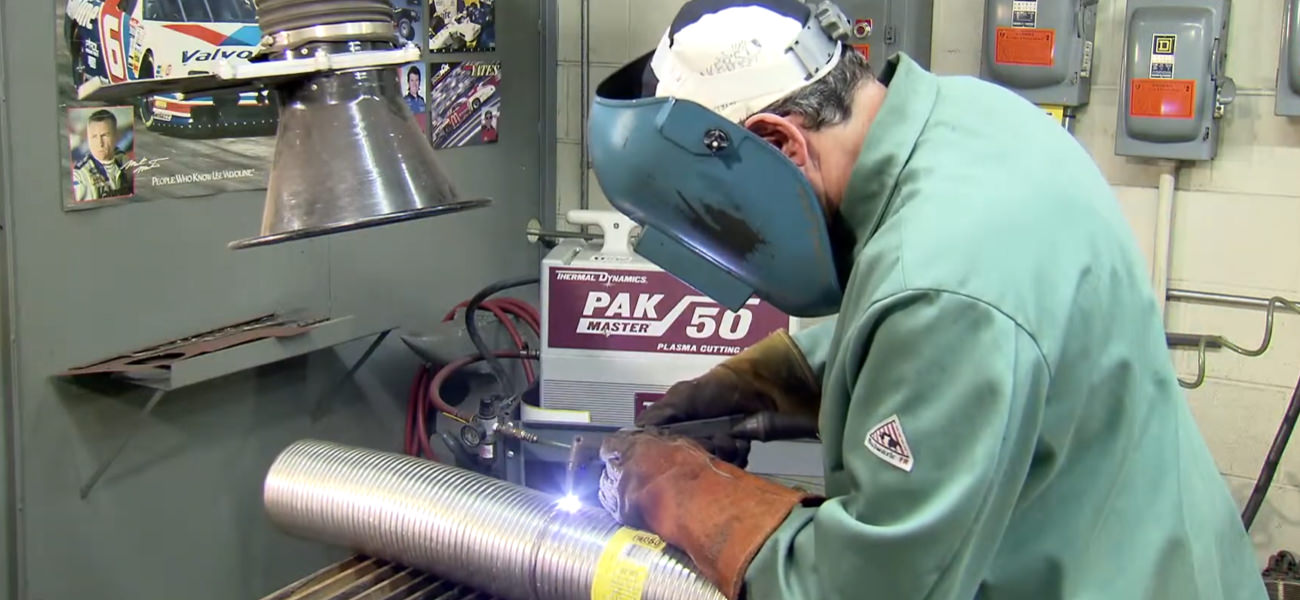
Chop saw – Leaves a smooth edge but some deburring may be required.
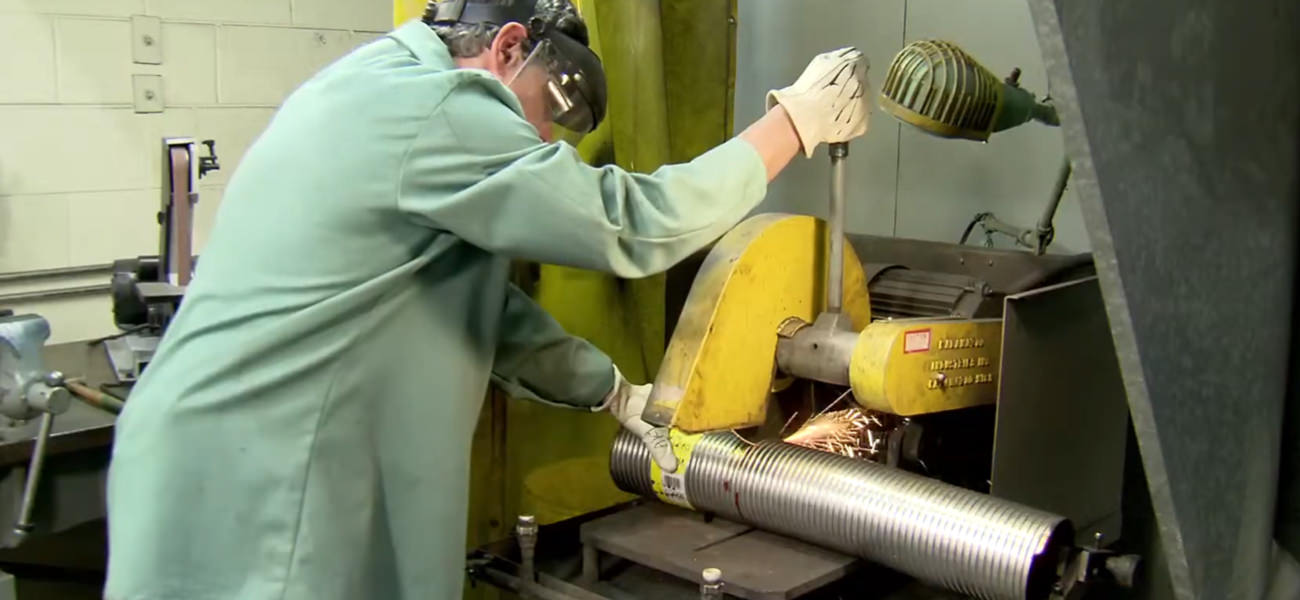
Band hacksaw – Leaves a rough edge that may require trimming and deburring. If trimming is required, bend the excess until it breaks or use cutting shears. If deburring is required, use a hand-operated sander or file or cut surfaces.
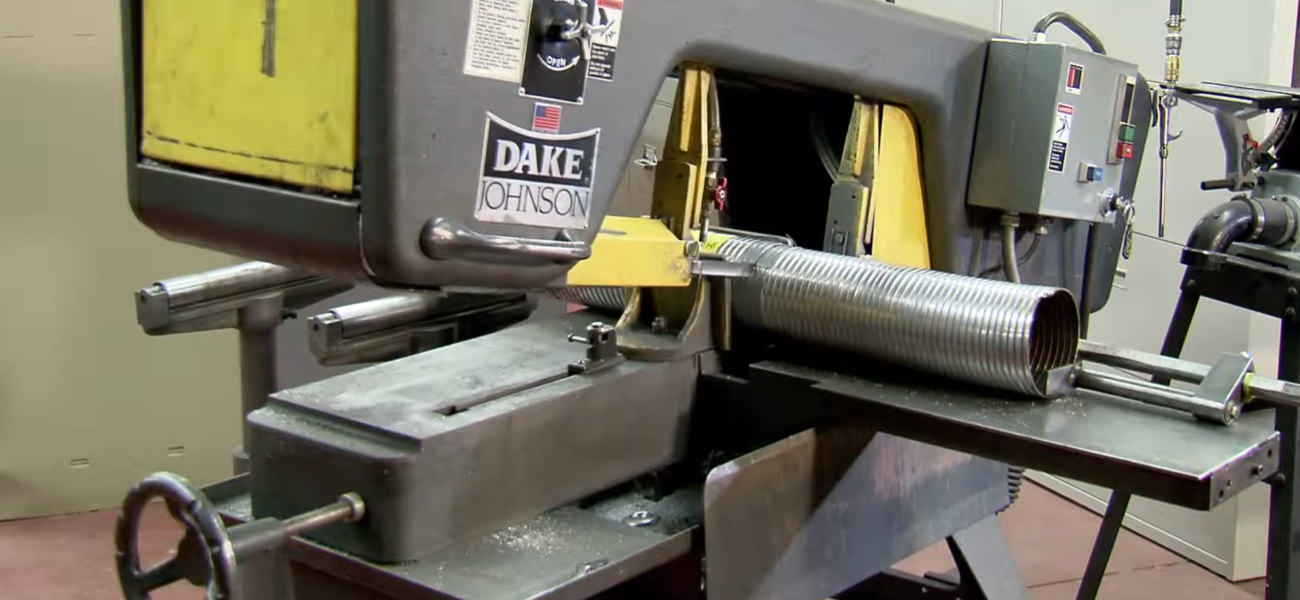
Installing Flex Pipe Tips
For optimal results, install tubing in its natural lie state – midway between fully compressed and fully extended. Doing this provides the most workable range and the longest service life of the installed flex
tubing.
To determine natural lie:
• Fully compress the flex pipe
• Bend the tube as much as possible against the edge of your workbench.
• Push the entire tube against the table until straight to reach its half extension or natural lie.
Keep in mind these tips:
• Use stainless steel in high heat areas like the turbo outlet.
• Avoid severe angles – flex pipe isn’t intended to replace elbows.
• Walker Mega-Clamps should be used for flex pipe connections.
Learn more about QUALITY EXHAUST PARTS, FIND THE RIGHT CAR PART, or FIND A LOCAL REPAIR SHOP TODAY.
The content in this article is for informational purposes only. You should consult with a certified technician or mechanic if you have questions relating to any of the topics covered herein. Tenneco will not be liable for any loss or damage caused by your reliance on any content.